
How to fix your washing machine
We explain how to fix six common washing machine faults.

I’ll wager that your washing machine is unloved.
It’s most likely tucked away in the laundry and cleaned reluctantly and rarely. Yet it’s expected to remove the grime of life on a daily basis without fuss. Everything is fine and dandy until, one day, it isn’t, and your dirty clothes start piling up.
So, what goes wrong with a washer and what can you do to keep yours spinning? The good news is that you can cheaply and easily repair most common faults.
Percentages are the proportion of faulty machines reported in our latest reliability survey that exhibited the particular problem.
Before you start
- If you’re not keen on tackling the repair yourself, enlist the services of a local specialist. They can access spare parts that can be hard to locate, and you won’t be left rueing your over-ambition as they’ll guarantee their work should something go wrong.
- Most washers report an error code when something goes wrong. Deciphering the code will help point you to the fault. The manual should explain the codes, otherwise you can likely find it online (just search the code and your brand/model).
It won’t turn on
Electronic circuits 25%, Controls not working 14%
Have you checked the machine is plugged in, switched on at the wall, and the fuse hasn’t blown or the circuit breaker tripped?
Next, make sure the door or lid has shut properly. Most front loaders have an interlock that confirms the door is closed. If the interlock has failed, it’s relatively simple to replace. Top loaders have a lid switch that does the same job.
If you’re unlucky, the control board or power supply is cooked (though these are relatively rare faults). Those are expensive parts to replace, and you’ll need to call in an expert.
You can’t open the front-loader door
Check the machine isn’t stuck mid-cycle, that any child lock function hasn’t been inadvertently switched on and there’s no water sitting in the drum. If these pass muster, you may have a broken door handle. It should be a cheap and easy repair (though some machines need a whole new door).
The drum won’t empty
Not draining 21%
Inside the machine, water from the drum flows through a sump hose, a filter (if your machine has one), then the pump, before exiting through the drain hose.
You can use gravity to drain water without the pump – unplug the drain hose and make sure it is lower than the drum. If it doesn’t drain, it’s likely you have a blocked hose or filter.
If the pump’s kaput, it doesn’t mean the whole machine is ready for the scrapheap – pumps aren’t expensive and can be replaced relatively easily.
The drum’s not turning
Not spinning 12%, Out of balance 11%, Motor broken 8%
The wash cycle runs, but the drum doesn’t spin. You might notice because your clothes are soaking wet after a programme has finished.
First, check the load isn’t too big or small – both can result in the drum getting unbalanced while spinning. To prevent damage, some machines won’t spin an unbalanced load.
If the drum isn’t turning during the wash or spin cycle, check the motor belt hasn’t broken or slipped off – when you rotate the drum by hand you should feel some resistance to it turning (that’s the belt turning the motor). A belt is an easy fix.
A less likely cause is worn motor brushes. These consumable parts wear down over time. If your machine is older than five years, you may need to replace them. New brushes are cheap, though you may need to remove the motor to fit them. Least likely of all is a broken motor or control module. Those are expensive and need specialist repair expertise.
It’s making an awful noise
Noisy 12%, Bearings 7%
First, work out what type of noise it is and where it’s coming from.
If the noise is coming from low down, sounds like a loud rattle, and only happens when water is being drained, you could have something stuck in the pump or filter. Most of the time, the pump will push these objects out with the water, but sometimes they lodge and can cause damage.
Bearing failures cause a grinding sound when the drum spins. Bearings should be a relatively simple replacement, but many are now built into the drum assembly, which makes them impossible to repair economically. Bearing failures are rare, though. To confirm, try turning the drum by hand – it should turn smoothly with little noise.
Leaks
Leaks contributed to a mere 6% of faulty machines in our survey. That’s probably because we only asked about failures in washers less than five years old. As rubber hoses and seals get older, we’d expect them to figure more prominently in the stats.
You should check water supply hoses periodically for signs of cracking, and replace them every five years to prevent a flooding disaster. Regularly examine the door seal for damage and cracking. If you need to replace a failing (or mouldy) door seal, it’s a surprisingly cheap and easy job.
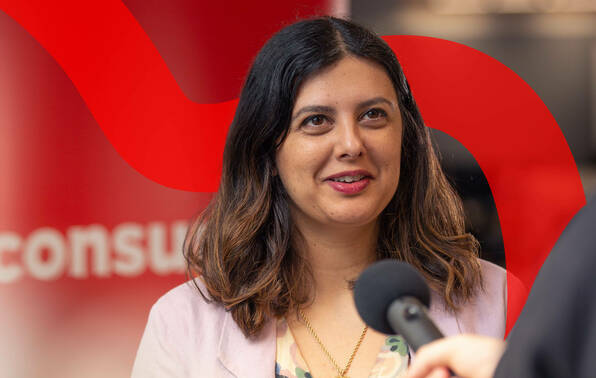
We can't do this without you.
Consumer NZ is independent and not-for-profit. To help us get a fairer deal for all New Zealand consumers, you can make a donation. We’ll use your contribution to investigate consumer issues and work for positive change.
Member comments
Get access to comment